Flugfertige Antenne im Pulverbettverfahren
Thales Alenia Space ist ein französischer Luft- und Raumfahrthersteller, der seit mehr als 40 Jahren eine bedeutende Rolle in der Weltraumforschung spielt. Da neue Technologien eine neue Ära der Weltraumforschung einläuten, wird die Verkürzung der Gesamtvorlaufzeit und die Erhöhung des Durchsatzes besonders wichtig, um auf dem wachsenden Markt wettbewerbsfähig zu bleiben. In dieser Fallstudie erfahren Sie, wie Thales mit dem FormUp 350 und dem Aluminium AS7 seine Ziele in der additiven Fertigung erreicht hat.
INDUSTRIE
Raumfahrt
HERAUSFORDERUNG
Entwurf und Bau einer monolithischen Antenne unter Verwendung additiver Fertigung, die die ECSS-Qualifikationen erfüllt und das Ziel des Kunden unterstützt, die TRL-3-Reife für additiv gefertigte Antennen zu erreichen.
KEY BENEFITS
- Globale Verzerrungen der Antenne: ±0,3 mm
- Gewicht reduziert: weniger als 600 g
- Produktionsrate: 1 Antenne/Tag/Maschine
- Reduzierte Nachbearbeitung
Verkürzte Vorlaufzeit
Kreative Form
In einem Stück gedruckt
Dünne Wände
Geschichte
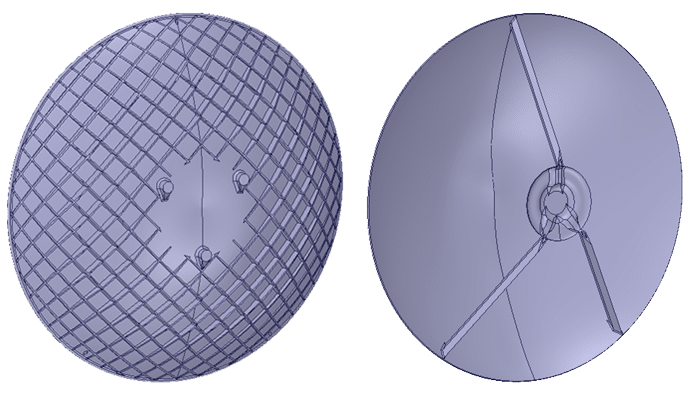
Normalerweise stellt Thales Alenia Space diese Art von Antenne aus mehreren Teilen her. Anschließend werden die einzelnen Teile in komplexen und zeitaufwändigen Schritten miteinander verbunden oder verschraubt. Die Herstellung präziser Komponenten ist zwar nicht so schwierig, aber ihre Montage zu einer präzisen Antenne ist zeitaufwändig und hat erhebliche Auswirkungen auf die globale Vorlaufzeit und den Durchsatz bei der Serienproduktion. Aus diesem Grund hat sich Thales für die additive Fertigung als Lösung entschieden.
Herausforderung
Entwicklung einer Antenne mit einem Durchmesser von 325 mm und einer Wandstärke von 1 mm durch additive Fertigung, um minimale Verzerrungen und eine Oberflächenbeschaffenheit zu gewährleisten, die den Standards für „flugfertige“ Produkte entspricht, ohne dass eine Nachbearbeitung erforderlich ist. Durch die Erfüllung dieser Standards wird TAS in der Lage sein, einen Technology Readiness Level (TRL) 3 für additiv gefertigte Cassegrain-Antennen zu erreichen.
Lösung
AddUp arbeitete eng mit Thales Alenia Space zusammen, um eine Simulation der Gegenverformung zu erstellen.
Zunächst wurde ein leichtes Design auf der Grundlage der ursprünglichen Spezifikationen erstellt: Haupt- und Nebenreflektorflächen, verfügbarer Bauraum, Lokalisierung der Schnittstellen. Als Nächstes wurde eine Isogitterstruktur auf der Rückseite des Hauptreflektors entworfen, um dem System mehr Steifigkeit zu verleihen. Anschließend wurde eine numerische Simulation durchgeführt, um die Verzerrungen der Antenne während der Produktion zu antizipieren.
Schließlich wird aus der ersten Simulation eine Datei mit der Gegenverformung erstellt. Ziel ist es, das ursprüngliche Design in die entgegengesetzte Richtung der simulierten Verzerrungen anzupassen. Während der Produktion heben sich die Verzerrungen aufgrund der internen Einschränkungen und des gegenverformten Designs gegenseitig auf, sodass das reale Teil so nah wie möglich am ursprünglichen Design bleibt.
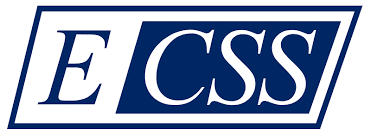
Um die beste Oberflächenbeschaffenheit zu erzielen, die nur minimale Nachbearbeitung erfordert, verwendeten AddUp und Thales Alenia Space ihr nach ECSS qualifiziertes Rezept auf der FormUp 350 in Aluminium AS7.
Die Leistung dieses Rezepts, in Verbindung mit den 4 Vollfeldlasern der Maschine, ermöglicht außerdem eine hohe Produktivität. Von AddUp durchgeführte Serienproduktionssimulationen zeigen eine Produktionsrate von mehr als 2 Antennen pro Tag und Maschine.
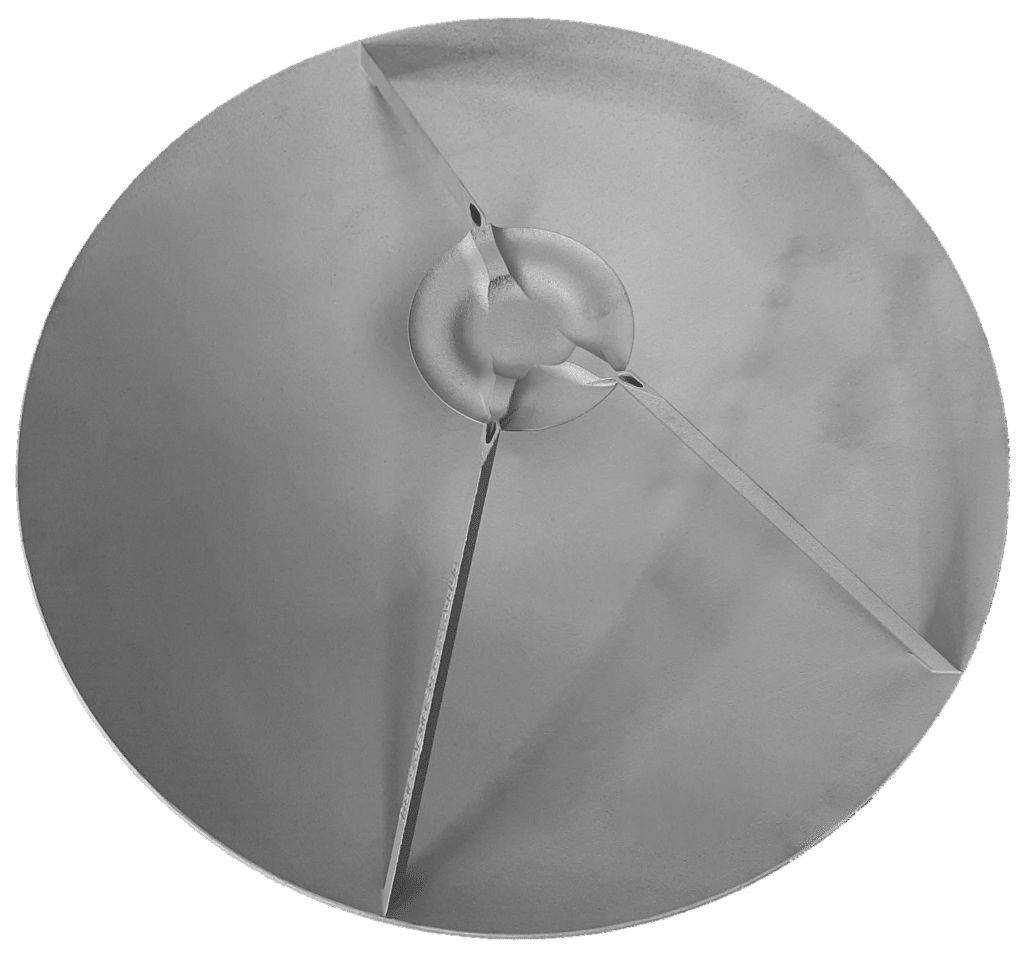
Results
Das endgültige Design erreichte eine leichte Antenne mit einem Gewicht von nur 385 Gramm. Die Isogitterstruktur wurde sorgfältig optimiert, um das Gewicht zu minimieren, indem die Größen um den Reflektor herum variiert wurden, wodurch nur die erforderlichen Bereiche verstärkt wurden. Die Verbindungsarme zwischen dem Hauptreflektor und dem Subreflektor wurden so konstruiert und gestaltet, dass die Kopplungseffekte im Nahfeld minimiert werden, wodurch die Gesamtleistung der Antenne im Fernfeld optimiert wird. Die Verzerrungen wurden erfolgreich minimiert, mit einer Abweichung von ±0,3 mm über 90 % der Antenne, was von beiden beteiligten Parteien positiv aufgenommen wurde. Darüber hinaus erfüllte die globale Oberflächenbeschaffenheit und -rauheit das Ziel von Ra 6,3 für beide Reflektoren und erzielte ein vollkommen zufriedenstellendes Ergebnis.
Erfahren Sie hier mehr über die FormUp 350 ECSS-Qualifizierung von Thales 3D Morocco.