Lesen Sie, wie AddUp’s Walzenüberzieher und die feinere Pulverpartikelgrößenverteilung (PSD) feinere Eigenschaften und eine verbesserte Oberflächengüte bieten und den Bedarf an Stützen bei der Herstellung eines statischen Mischers eliminieren.
Written by: Nick Estock, Director of Applications and Business Development
Die additive Fertigung hat, wie jedes Herstellungsverfahren, ihre Stärken und Schwächen. Alle Verfahren haben in der Regel wertsteigernde Schritte und notwendige sekundäre Operationen, die eine Folge ihrer Unzulänglichkeiten sind. Stützstrukturen sind eines dieser notwendigen Übel von AM. Sie sind Teil des Prozesses, tragen aber nicht zur Wertschöpfung des fertigen Teils bei. Vielmehr mindern sie den Wert, da Stützstrukturen Material und Maschinenzeit verbrauchen und nach dem Druck wieder entfernt werden müssen. All dies verringert die Produktivität und kostet Sie letztendlich Geld. Schaffen wir sie also ab! (OK, vielleicht minimieren wir sie…)
AddUp, ein Gemeinschaftsunternehmen von Michelin und Fives, hat ein System entwickelt, das genau das ermöglicht. Michelin setzt AM bereits seit Anfang der 2000er Jahre ein, lange bevor ich überhaupt wusste, was ein 3D-Drucker ist (als ich in der High School war, gab es weder 3D-Drucker noch Smartphones). Michelin nutzte die Technologie zunächst, um den Entwicklungszyklus für seine Reifenformeinsätze, die sogenannten Sipes, zu verkürzen. Heute werden jährlich über eine Million dieser Lamellen für ihre Produktionsformen hergestellt. Entscheidende Merkmale dieser Lamellen sind: eine Auflösung von bis zu 0,2 mm, flache Überhänge von bis zu 15 Grad und eine Oberflächengüte von bis zu 4 Ra um, wie gedruckt.
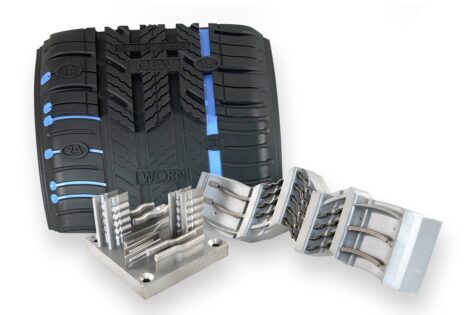
Als Michelin dieses Joint Venture mit Fives einging, wie konnte man da ein so hohes Qualitätsniveau erreichen? Durch die Entwicklung des FormUp 350 als einzigem industrielle Pulverbettfusionsmaschine (Powder Bed Fusion, PBF) zur Verwendung eines Walzenbeschichters in Verbindung mit einer feineren Pulverpartikelgrößenverteilung (PSD). Typische PBF-Technologien verwenden eine PSD von 25-63 um. Der FormUp kann Pulver mit einer Partikelgröße von 5-25 um effektiv verwalten, verteilen und ausbringen. Durch die Verwendung von feineren Pulvern und einer Walze erreicht AddUp eine bessere Packungsdichte des Aufbaubetts von bis zu 70 %. Kombinieren Sie dies mit hochqualitativen offenen Parametern und Sie haben ein Rezept für die Herstellung feinerer Eigenschaften, bessere Oberflächen und ja, weniger Stützen, problemlos und sofort nach dem Auspacken! Was meine ich mit „sofort einsatzbereit“? Ich meine damit, dass es keine geheime Sauce gibt, dass keine speziellen Parameter in bestimmten Bereichen angewendet werden und dass der Prozess nicht verlangsamt wird. Entwerfen Sie es, wenden Sie Ihre Standardparameter an, laden Sie es auf die Maschine und los geht’s!
Schauen wir uns ein Beispiel an, einen statischen Mischer, den unser Anwendungsteam entwickelt hat, um diesen Punkt besser zu veranschaulichen.
Was ist ein Statikmischer?
Wikipedia definiert dies als:
„Ein statischer Mischer ist ein präzisionsgefertigtes Gerät zum kontinuierlichen Mischen von flüssigen Stoffen ohne bewegliche Komponenten.[1] Normalerweise sind die zu mischenden Flüssigkeiten flüssig, aber statische Mischer können auch zum Mischen von Gasströmen, zum Dispergieren von Gas in Flüssigkeit oder zum Mischen nicht mischbarer Flüssigkeiten verwendet werden.“
Mit anderen Worten, es handelt sich um ein Rohr, in das zwei oder mehr Flüssigkeiten am Einlass eingeleitet und durch eine Reihe von „statischen“ Elementen wie Platten oder Schaufeln geleitet werden, um d i e Flüssigkeiten am Ausgang zu homogenisieren. Warum ist dies eine großartige Additivanwendung? Weil man das Design für jede beliebige Anwendung optimieren und anpassen kann. Warum ist ein statischer Mischer ein schwer additiv herstellbares Teil? Weil die Mischelemente ein Problem darstellen, wenn sie nach herkömmlichen AM-Richtlinien gedruckt werden. Die Standard-Designrichtlinien für AM bedeuten, dass diese Elemente im 45- Grad-Winkel gedruckt werden müssen. Diese Einschränkung würde bedeuten, dass man entweder den Mischbereich des Mischers selbst verlängern und/oder viele weitere Elemente hinzufügen müsste, um die gewünschte Leistung zu erzielen. Beide Optionen bedeuten, dass man die Vorteile der additiven Fertigung nicht mehr nutzen kann und ein ineffizientes, teures Teil übrig bleibt.
Statischer Mischer mit: | AddUp Statischer Mischer | Standard-AM-Richtlinien (45˙-Lamellen) | Ermäßigun g |
---|---|---|---|
Gesamthöhe | 305 mm | 654 mm | 53% |
Benötigtes Material | 738.5 cc | 1583.82 cc | 53% |
Bauzeit | 88 Stunden, 32 Minuten | 189 Stunden, 51 Minuten | 53% |
Der AddUp Static Mixer steigerte die Produktivität um 53%!
Was aber, wenn Sie diese Einschränkung nicht hätten?
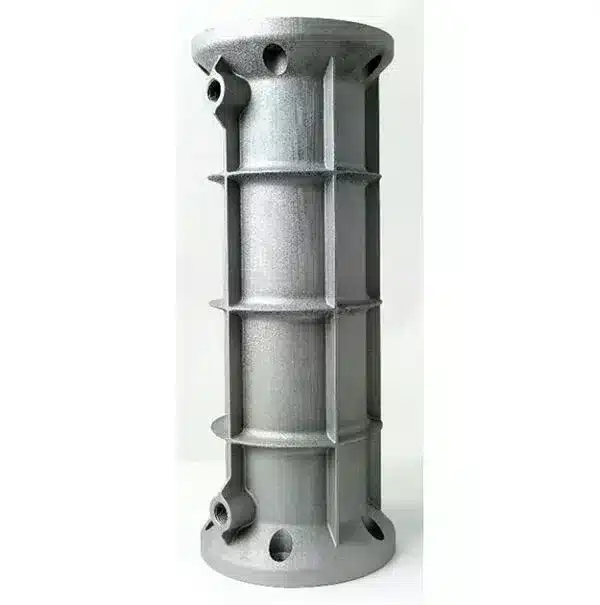
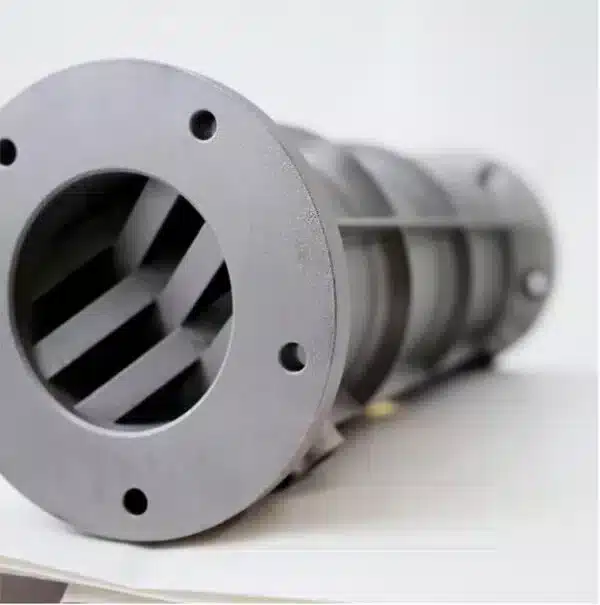
Der hier gezeigte statische Mischer wurde ohne diese Einschränkungen gedruckt. Unsere Ingenieure entwarfen diesen Mischer mit bis zu 25 Grad flachen Elementen ohne Stützen und erreichten dennoch eine akzeptable Oberflächengüte. Und nicht nur das: Sie haben ihn in weniger als zwei Wochen entworfen und zum ersten Mal ein Ergebnis erzielt. Wie war das möglich? Die Walzen- und Feinpulverkonfiguration von AddUp in Verbindung mit robusten Parametern bieten neue Designfreiheiten für den AM-Prozess.
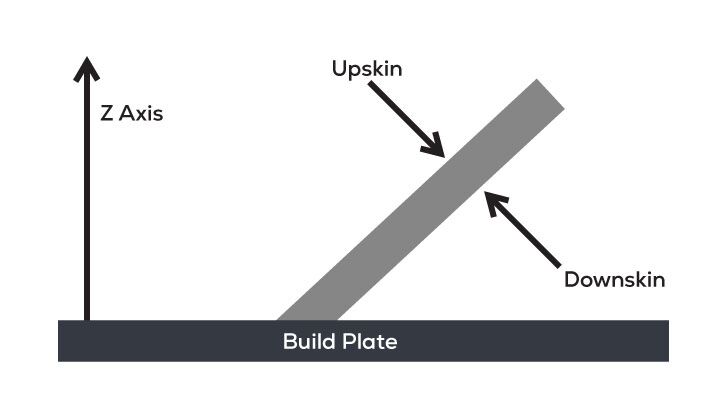
Wie in den Exponaten A und B gezeigt, kann das AddUp-System bei Verwendung eines Walzensystems in Verbindung mit feinerem Pulver eine Verringerung der Oberflächenrauhigkeit um etwa 10 Ra um für jeden gegebenen Aufwärts-/Abwärtswinkel im Vergleich zu PSDs mit mittlerem Pulver und einer Konfiguration mit Klingenüberzieher erreichen.
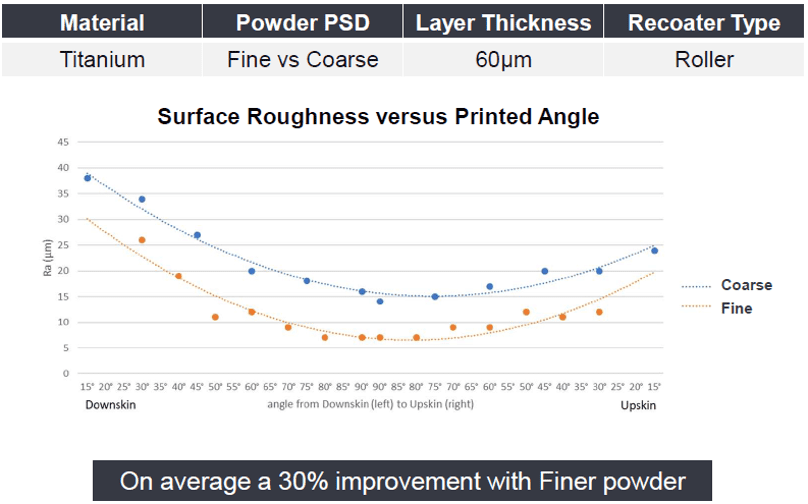
EXHIBIT A
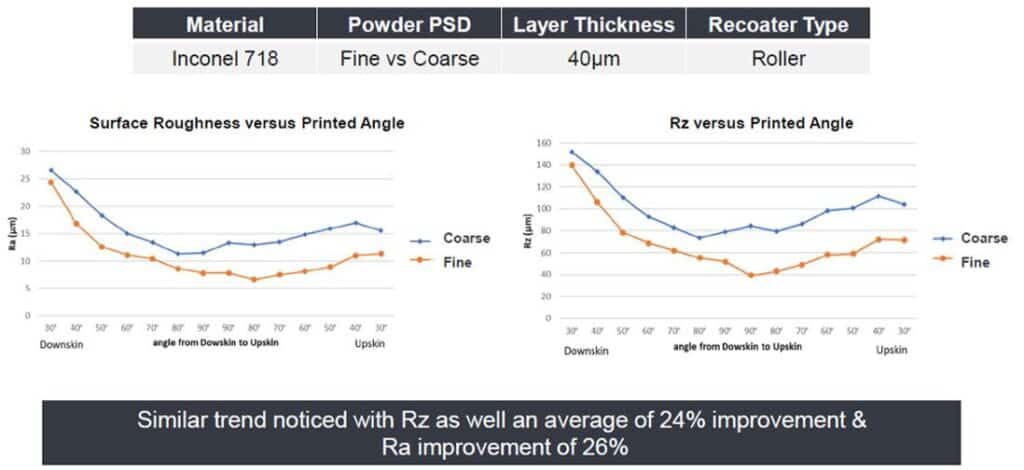
EXHIBIT B
Vergessen Sie nicht, dass dies direkt nach dem Auspacken und problemlos möglich war! Es gibt keine speziellen Downskin-Parameter. Es ist keine fortgeschrittene Entwicklung erforderlich, die Monate und unzählige Stunden an Entwicklungs- und Maschinenzeit in Anspruch nehmen kann, um dies zu erreichen. Diese Ergebnisse können mit unseren standardmäßigen, hochproduktiven Volumen- und Konturparametern erzielt werden. Bei anderen Maschinenherstellern gehen verbesserte Oberflächengüten oder extreme Auskragungen oft mit einer Verlangsamung der Produktivität einher. Das liegt daran, dass sie weniger Laserleistung bei einer geringeren Geschwindigkeit verwenden, um solche Ergebnisse zu erzielen, was Ihre Produktivität verlangsamt. Dies führt auch zu zusätzlichen Variablen bei d e n mechanischen Eigenschaften Ihres Teils. Anstelle eines einzigen Parametersatzes, der über das gesamte Volumen I h r e s Bauteils hinweg bekannte mechanische Eigenschaften liefert, haben Sie Bereiche geschaffen, die potenziell unterschiedliche Verhaltensweisen aufweisen können. Das AddUp-System erreicht diese Ergebnisse dank einer besseren Packungsdichte unseres Pulverbettes und unserer Walze mit feiner Pulverkonfiguration.
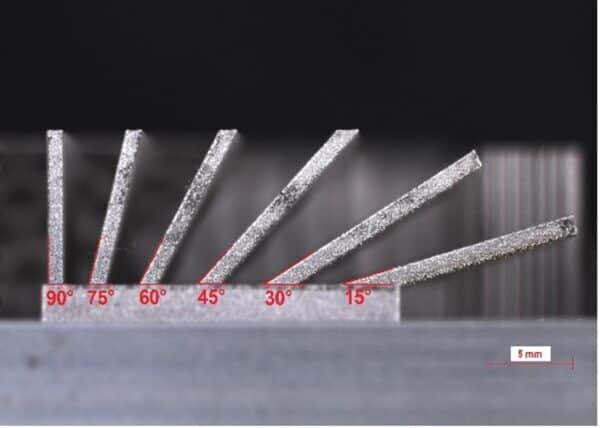
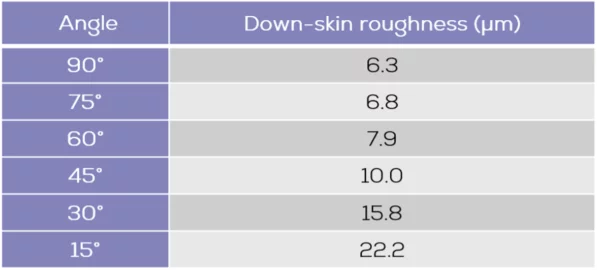
Sie denken, das ist alles zu schön, um wahr zu sein? Testen Sie mich! Wir haben gerade die Renovierung unserer Anlage in Cincinnati abgeschlossen, die nicht nur als Hauptsitz in den USA dient, sondern auch als technisches Demonstrationszentrum. Vom Pulver bis zum Bauteil verfügt unsere Werkstatt über alle Möglichkeiten, um Benchmarks, Funktionsprototypen und sogar Produktionsteile herzustellen. Unser Team ist bereit, unsere Kunden zu unterstützen, die gerade erst in das AM einsteigen, bis hin zu einer schlüsselfertigen, industrialisierten Anwendung.
Nutzen Sie das untenstehende Formular, um uns von Ihrem Projekt zu erzählen und wir zeigen Ihnen den AddUp Unterschied! Wir freuen uns auf die Gelegenheit, Ihre Anwendungen zu „ent-supporten“!