Antenne prête pour le vol dans un lit de poudre Fusion
Thales Alenia Space est un constructeur aérospatial français qui joue un rôle important dans l’exploration spatiale depuis plus de 40 ans. Alors que les nouvelles technologies ouvrent la voie à une nouvelle ère d’exploration spatiale, la réduction du délai global et l’augmentation de la production deviennent particulièrement importantes pour rester compétitif sur ce marché en pleine croissance. Découvrez dans cette étude de cas comment Thales a utilisé la FormUp 350 et l’AS7 en aluminium pour atteindre ses objectifs de fabrication additive.
INDUSTRIE
Espace
CHALLENGE
Concevoir et construire une antenne monolithique en utilisant la fabrication additive qui répond aux qualifications ECSS et soutient l’objectif du client d’atteindre la maturité TRL 3 pour les antennes fabriquées de manière additive.
KEY BENEFITS
- Distorsions globales de l’antenne : ±0,3 mm
- Poids réduit : moins de 600 gr
- Taux de production : 1 antenne /jour /machine
- Réduction du post-traitement
Réduction du délai d’exécution
Forme créative
Imprimé en une seule pièce
Murs minces
L’ Historie
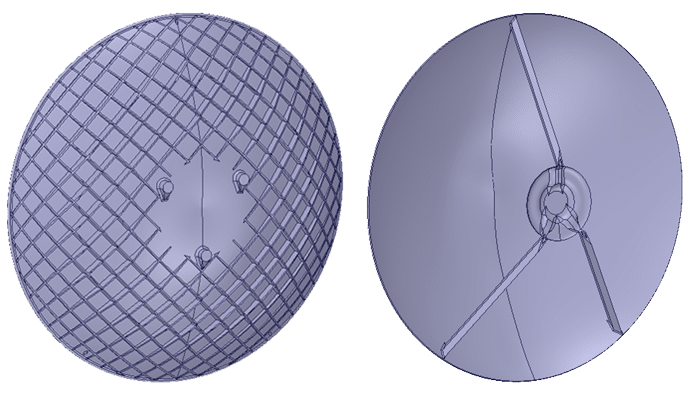
En général, Thales Alenia Space fabrique ce type d’antenne en plusieurs parties. Chaque pièce est ensuite collée ou boulonnée au cours d’étapes complexes et coûteuses. Si la fabrication de composants précis n’est pas si difficile, leur assemblage en une antenne précise prend du temps et a un impact majeur sur le délai global et le débit de la production en série. C’est pourquoi Thales s’est tourné vers la fabrication additive comme solution.
Défi
Développer une antenne de 325 mm de diamètre avec une épaisseur de paroi de 1 mm par fabrication additive, en garantissant des distorsions minimales et une finition de surface répondant aux normes « prêt à voler » sans nécessiter de post-traitement. En respectant ces normes, TAS sera en mesure d’atteindre un niveau de préparation technologique (TRL) 3 pour les antennes Cassegrain fabriquées de manière additive.
Solution
AddUp a travaillé en étroite collaboration avec Thales Alenia Space pour fournir une simulation contre-déformée.
Tout d’abord, une conception légère a été générée autour des spécifications initiales : surfaces des réflecteurs principaux et secondaires, espace de conception disponible, localisation des interfaces. Ensuite, une structure isogrid a été conçue à l’arrière du réflecteur principal pour ajouter de la rigidité au système. Ensuite, une simulation numérique a été réalisée pour anticiper les déformations de l’antenne pendant la production.
Enfin, un fichier contre-déformé est obtenu à partir de la simulation initiale. Le but est d’adapter le design original dans la direction opposée aux distorsions simulées. Lors de la production, les distorsions dues aux contraintes internes et au design contre-déformé s’annulent, ce qui permet de maintenir la pièce réelle aussi proche que possible du design original.
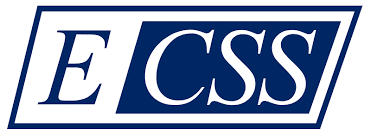
Afin d’obtenir la meilleure finition de surface, nécessitant un post-traitement minimal, AddUp et Thales Alenia Space ont utilisé leur recette qualifiée ECSS sur le FormUp 350, en aluminium AS7.
La performance de cette recette, couplée aux 4 lasers plein champ de la machine, permet également une productivité élevée. Les simulations de production en série réalisées par AddUp montrent un taux de production de plus de 2 antennes par jour et par machine.
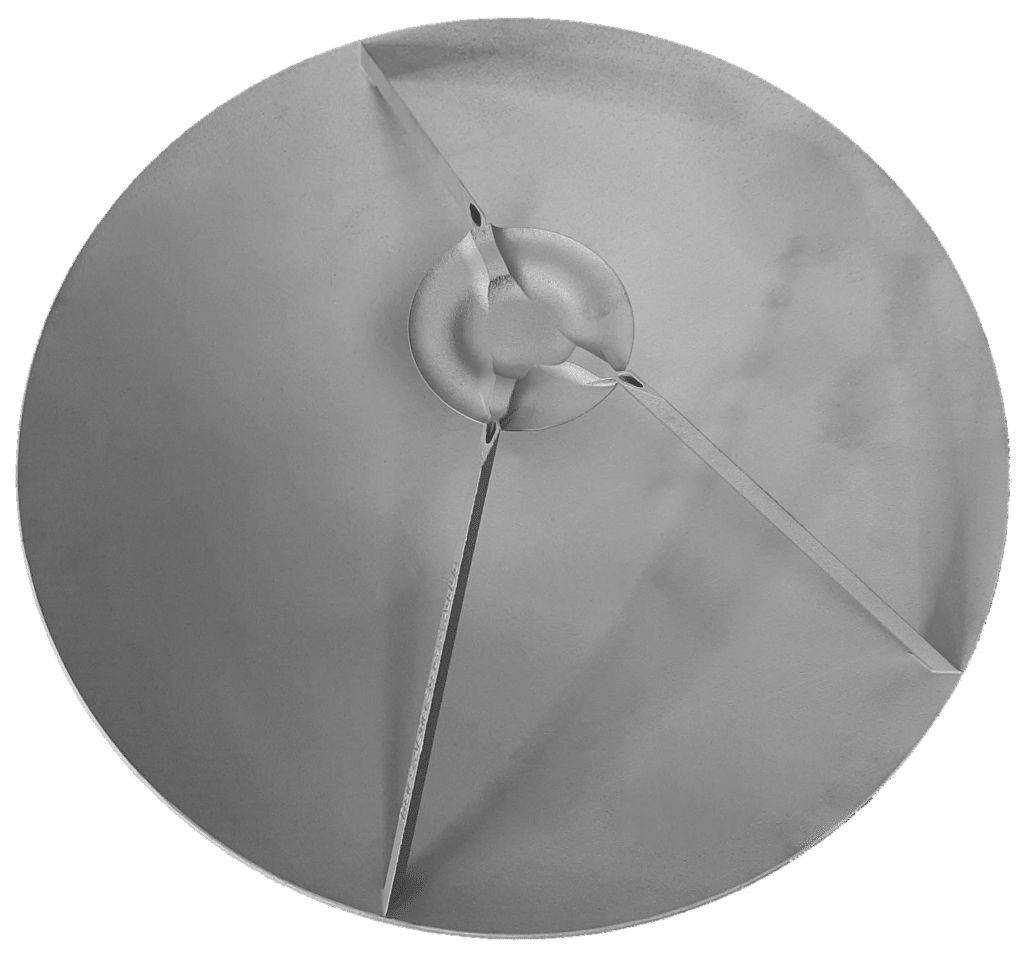
Résultats
La conception finale a permis d’obtenir une antenne légère, pesant seulement 385 grammes. La structure isogrid a été méticuleusement optimisée pour minimiser le poids en variant les tailles autour du réflecteur, renforçant ainsi uniquement les zones nécessaires. Les bras de connexion entre le réflecteur principal et le sous-réflecteur ont été conçus pour minimiser les effets de couplage en champ proche et optimiser les performances globales de rayonnement de l’antenne en champ lointain. Les distorsions ont été minimisées avec succès, avec un écart de ±0,3 mm sur 90 % de l’antenne, ce qui a été bien accueilli par les deux parties concernées. En outre, l’état de surface global et la rugosité ont atteint l’objectif de Ra 6,3 pour les deux réflecteurs, ce qui a permis d’obtenir un résultat tout à fait satisfaisant.
Pour en savoir plus sur la qualification FormUp 350 ECSS de Thales 3D Maroc, cliquez ici.