L’interview du directeur des technologies additives de Zeda montre comment la flexibilité de la plateforme FormUp 350 permet de développer des applications difficiles et de maximiser la productivité. Le partenariat avec AddUp est motivé par un objectif commun de production de pièces à grande échelle et par un engagement en faveur d’une collaboration ouverte.
Alors que le partenariat entre AddUp et Zeda continue de se développer, Rachel Levine, directrice des technologies additives chez Zeda, nous explique comment la flexibilité de la FormUp 350 l’aide à développer des applications difficiles et à maximiser la productivité.
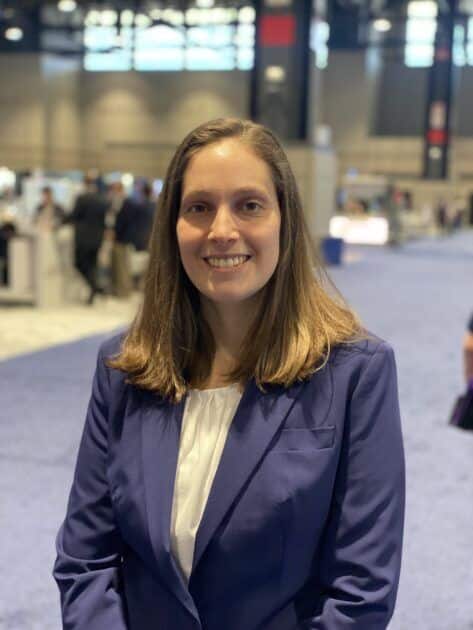
1. Pourquoi êtes-vous passionné par la fabrication additive?
En première année d’université, j’ai suivi un cours intitulé « Rapid Prototyping » (prototypage rapide). À partir de ce moment-là, je suis devenu accro. Jusqu’à ce moment-là, je pensais que j’allais rejoindre l’industrie du jouet après avoir obtenu mon diplôme, car j’avais déjà commencé à poursuivre cette carrière dans le cadre d’un programme d’enseignement coopératif le semestre précédent. Une fois que j’ai vu le potentiel de la technologie additive, je n’ai pas pu retourner dans une industrie qui s’appuyait sur des technologies plus anciennes et établies. Ce que je préfère dans la technologie additive, c’est qu’il y a encore tellement d’applications inexplorées… il y a encore de nouvelles frontières que seule une poignée de personnes dans le monde ont vraiment les connaissances, les ressources et les compétences nécessaires pour explorer.
2. Qu’est-ce qui vous enthousiasme dans le partenariat avec AddUp et la plateforme FormUp 350 ?
Ce partenariat est une nouveauté à bien des égards. Nos équipes travaillent ensemble depuis près d’un an, et j’ai rarement eu le plaisir de travailler avec une autre entreprise qui est vraiment prête à s’engager dans un partenariat qui vise un plus grand objectif. Trop souvent, les partenariats sont limités par la méfiance et la réticence à partager des informations, mais l’équipe d’Addup s’est vraiment engagée dans le partenariat avec des esprits ouverts et un objectif partagé de conduire à la production de pièces à grande échelle. Sans oublier que le FormUp ouvre la voie à des améliorations de la productivité grâce à sa configuration laser quadruple, ses paramètres ouverts et son filtre à longue durée de vie.
3. Comment les paramètres ouverts d’AddUp Manager aident-ils les ingénieurs de Zeda à atteindre leurs objectifs ?
Les bons paramètres font toute la différence en matière de productivité, de constructibilité, de qualité et de propriétés des matériaux. Zeda comprend que la production médicale à haut volume et à caractéristiques fines peut nécessiter des paramètres différents de ceux des pièces spatiales de grande taille parce qu’ils doivent être optimisés pour des exigences différentes. La possibilité de modifier les paramètres pour les treillis ou d’autres caractéristiques spécialisées est quelque chose que nous espérons exploiter à l’avenir. Bien entendu, tous les paramètres doivent être validés et qualifiés en fonction des besoins du produit, un processus que nous connaissons bien.
4. En quoi la FormUp350 diffère-t-elle des autres plates-formes sur le marché ?
La FormUp350 est l’une des seules machines sur le marché à pouvoir exécuter à la fois la coupe de poudre LPBF typique et une coupe de poudre beaucoup plus fine. Cela nous donne la flexibilité nécessaire pour répondre à certaines applications difficiles que nous pourrions rencontrer à l’avenir. J’ai également reçu récemment un aperçu de certains développements futurs qui me rendent encore plus enthousiaste quant à notre partenariat et aux avantages que nous pourrons apporter à nos clients.
5. Comment la plate-forme 350×350 et les 4 lasers de la FormUp débloquent-ils des applications pour les clients de Zeda ?
En tant que fabricant à façon, nous voyons une grande variété de pièces. Pour les petites pièces, le système quadruple laser à recouvrement plein champ de l’AddUp nous permet d’améliorer notre productivité. La taille de la plate-forme nous permet d’atteindre une gamme plus large de pièces plus grandes.
6. Quelle est l’importance de la gestion des poudres dans le processus global ?
Sans réutilisation des poudres, le coût d’AddUp devient prohibitif pour presque toutes les industries. Avec une validation et un contrôle de qualité appropriés, la boucle de poudre interne d’AddUp nous permet d’évoluer vers une réutilisation à l’infini. La validation de la durée de vie de la poudre dans le système interne d’AddUp est un projet clé dans lequel Zeda s’engagera avec AddUp.
7. En quoi le module de poudre autonome de FormUp change-t-il la donne pour Zeda ?
La réutilisation de la poudre devient un cauchemar à suivre une fois que la poudre quitte un système où elle peut être accidentellement exposée à l’humidité ou à un équipement contaminé. Pour les alliages tels que le titane, le mouvement de la poudre hors ligne et le processus de tamisage peuvent également être dangereux. Le système interne inerte de FormUp élimine les risques de contamination courants ainsi que les risques d’exposition et d’explosion pour l’opérateur.