Die FormUp 350 Powder Bed Fusion (PBF) Maschine revolutioniert die Herstellung von großen Wirbelsäulenfusionsgeräten und bietet eine höhere Effizienz, Präzision und Kosteneffizienz.
Einführung
Wirbelsäulenfusionsvorrichtungen spielen in der Medizin eine entscheidende Rolle, da sie bei Wirbelsäulenoperationen für die notwendige Unterstützung und Stabilität sorgen. Traditionell wurden große Wirbelsäulenfusionsvorrichtungen mit kleinformatigen Pulverbettfusionsmaschinen (Powder Bed Fusion, PBF) hergestellt oder aus Poly-Stangenmaterial gefräst. Diese Methoden waren zwar effektiv, brachten jedoch einige Herausforderungen mit sich, darunter hohe Kosten und lange Produktionszeiten. Das Aufkommen fortschrittlicher Fertigungstechnologien, wie z. B. der FormUp 350 PBF-Maschine, hat den Produktionsprozess jedoch revolutioniert und bietet höhere Effizienz, Präzision und bessere Patientenergebnisse.
Traditionelle Herstellungsmethoden: PBF und PEEK
Das herkömmliche Herstellungsverfahren für große Wirbelsäulenfusionsvorrichtungen stützte sich auf PBF oder die maschinelle Bearbeitung von PEEK- Stangenmaterial. Diese Methoden waren zwar effektiv, aber auch nicht ohne Nachteile. Der Produktionsprozess war langsam und kostspielig, was zu höheren Preisen für das fertige Implantat führte. Darüber hinaus fehlten bei der Herstellung von PEEK-Implantaten die idealen integrativen Osseo-Eigenschaften, die für den Erfolg des Implantats entscheidend sind. Darüber hinaus stellte die instabile Materiallieferkette für PEEK eine weitere Herausforderung im Herstellungsprozess dar.
Die Einführung der additiven Fertigung
Die Einführung der additiven Fertigung bedeutete einen bedeutenden Wandel in der Produktion von großen Wirbelsäulenfusionsgeräten. Die Herstellung dieser Geräte auf kleineren Plattformen mit 1-2 Lasern erhöhte jedoch die Kosten für das fertige Implantat. Diese Implantate waren groß in Z, was zu längeren Bauzeiten führte, die sich mit einer geringen Anzahl von Lasern noch weiter erhöhten. Darüber hinaus trugen die Verwendung eines Schaber-/Bürstenbeschichtungsprozesses und die Notwendigkeit der Drahterodierung (EDM) zum Entfernen der LLIFs von der Bauplatte zu den Gesamtproduktionszeiten und -kosten bei.
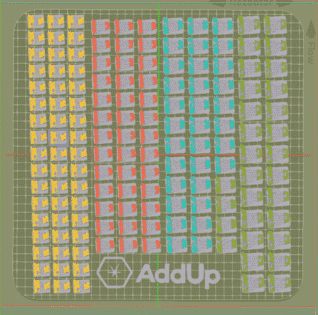
Das FormUp 350: Ein Sprung nach vorn bei der Herstellung von Wirbelsäulenfusionsgeräten
Die FormUp 350 PBF-Maschine hat sich als überlegene Alternative zu kleineren Plattformen mit 1-2 Lasern erwiesen. Dank einer 350 Millimeter großen quadratischen Bauplatte kann die FormUp 350 im Vergleich zu kleineren Plattformen die 1,5-fache Menge an großen Wirbelsäulenimplantaten aufnehmen. Durch den Einsatz von 4 Lasern können 152 große Wirbelsäulenimplantate in nur 32 Stunden gedruckt werden, was die Produktionszeit erheblich verkürzt und den Ausstoß erhöht.
Das FormUp 350 verwendet eine Pulverwalzen-Technologie, die geometrische Komplexität mit minimalen Stützen ermöglicht und zu einer optimalen Oberflächengüte führt. Mit dieser Technologie lassen sich komplexe Strukturen und Oberflächenrauhigkeiten realisieren, die zu besseren Patientenergebnissen beitragen. Es besteht keine Notwendigkeit mehr für ein plasmaporöses Spray oder eine trabekuläre Oberfläche auf Plattenbasis, und die Oberflächenrauhigkeit ist kein Nebenprodukt des Prozesses. Dies trägt dazu bei, die für die Fertigstellung eines Endprodukts erforderlichen Herstellungsprozesse zu verringern, was die Kosten in allen Teilen der Lieferkette senkt und effizientere Patientenergebnisse unterstützt.
Die Auswirkungen des FormUp 350 auf die Medizinprodukteindustrie
Der Einsatz des FormUp 350 bei der Herstellung von großen Wirbelsäulenfusionsgeräten hat weitreichende Auswirkungen auf die Medizinprodukteindustrie. Durch die Verkürzung der Vorlaufzeiten und die Erhöhung der Präzision können die Hersteller mit dem FormUp 350 schneller auf die Marktanforderungen reagieren und qualitativ hochwertigere Produkte herstellen. Darüber hinaus wird durch die Möglichkeit, komplexe Strukturen zu drucken und eine optimale Oberflächenrauheit zu erzielen, die Leistung der Implantate verbessert, was wiederum zu besseren Ergebnissen für die Patienten führt. Dies ist ein bedeutender Fortschritt, da er nicht nur die Lebensqualität der Patienten erhöht, sondern auch die Notwendigkeit von Revisionseingriffen verringert, was zu Kosteneinsparungen sowohl für die Patienten als auch für die Gesundheitsdienstleister führt.
Ergebnisse
Große Wirbelsäulenimplantate, die mit einer kleinen Baukapazität, einer geringen Anzahl von Lasern und herkömmlichen Wiederbeschichtungssystemen hergestellt werden, kosten mehr als solche, die mit dem FormUp 350 hergestellt werden.
Die FormUp 350 Maschine ist ideal für medizinische Anwendungen, da sie ein verbessertes und kosteneffizientes Verfahren für die Massenfertigung hochkomplexer und/oder kundenspezifischer medizinischer Teile bietet.
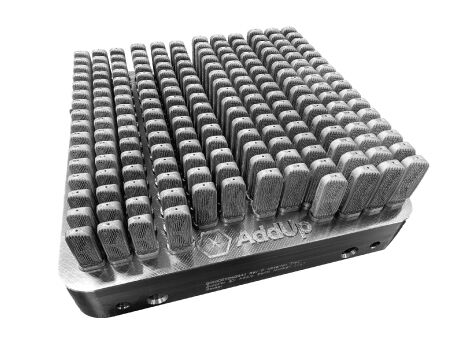
Per Laser gefertigte Teile auf dem FormUp 350:
- 2 Laser – 76
- 4 Laser – 38
Zeit, auf dem FormUp 350 aufzubauen:
- 2 Laser – 52,95
- 4 Laser – 32,35
Jährlicher Durchsatz auf dem FormUp 350:
- 1 Schicht pro Tag für
- 52 Wochen im Jahr