Mélangeur statique imprimé en 3D et sans support – blog
Découvrez comment le dispositif de recouvrement à rouleaux d’AddUp et la distribution granulométrique plus fine des poudres (PSD) permettent d’obtenir des caractéristiques plus fines, une meilleure finition de surface et éliminent le besoin de supports lors de la production d’un mélangeur statique.
Écrit par: Nick Estock, directeur des applications et du développement commercial
La fabrication additive, comme tout procédé de fabrication, a ses forces et ses faiblesses. Tous les processus comportent généralement des étapes à forte valeur ajoutée et des opérations secondaires nécessaires qui sont la conséquence de leurs défauts. Le supportage est l’un de ces maux nécessaires de la fabrication additive. Les supports de structure font partie du processus mais n’ajoutent aucune valeur à la pièce finale. En fait, ils diminuent cette même valeur car les supports consomment du matériel et du temps machine et doivent ensuite être retirés après impression. Tout cela réduit la productivité et, en fin de compte, vous coûte de l’argent. Alors, éliminons-les ! (OK, disons plutôt, minimisons-les…).
AddUp, une coentreprise entre Michelin et Fives, a mis au point un système pour y parvenir. Michelin utilise lla fabrication additive (AM) depuis le début des années 2000, bien avant que je sache ce qu’était une imprimante 3D (nous n’avions pas d’imprimantes 3D ni même de smartphones lorsque j’étais au lycée). Michelin a d’abord utilisé cette technologie pour réduire le cycle de développement des inserts de moulage de ses pneus, appelés lamelles. Aujourd’hui, ils produisent plus d’un million de ces lamelles par an pour leurs moules de production. Les caractéristiques essentielles de ces lamelles imprimées en 3D sont les suivantes : une résolution allant jusqu’à 0,2 mm, des surplombs peu profonds pouvant aller jusqu’à 15 degrés et une qualité de surface pouvant aller jusqu’à 4 Ra μm.
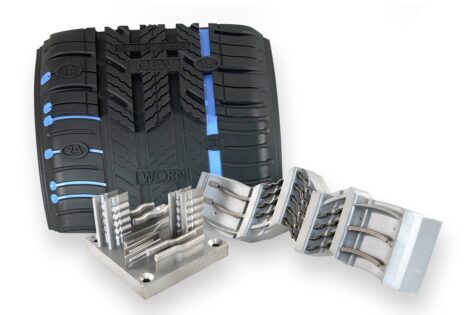
Lorsque Michelin s’est lancé avec Fives dans l’impression 3D métallique, comment ont-ils réussi à atteindre un tel niveau de qualité ? En développant la FormUp® 350, qui est la seule machine industrielle de fusion sur lit de poudre (PBF) à utiliser un rouleau en conjonction avec une distribution de la taille des particules de poudre plus fine. Les technologies PBF habituelles utilisent une taille allant de 25 à 63 μm. La FormUp peut quant à elle gérer, distribuer et étaler efficacement des poudres jusqu’à 5-25 μm. En utilisant des poudres plus fines et un rouleau, la FormUp obtient une meilleure densité de tassement sur son plateau de production, allant jusqu’à 70% de densité. Combinez cela avec des paramètres ouverts de haute qualité et vous avez une recette pour construire des caractéristiques plus fines, de meilleures finitions et oui moins de supports, sans tracas et dès la sortie de machine ! Qu’est-ce que je veux dire par « dès la sortie de machine » ? Je veux dire pas de sauce secrète, pas de paramètres spéciaux appliqués dans certaines zones et pas de ralentissement du processus. Concevez-le, appliquez vos paramètres standards, chargez-le sur la machine et c’est parti !
Prenons un exemple, un mélangeur statique que notre équipe d’application a développé pour mieux illustrer ce point.
Qu’est-ce qu’un mélangeur statique ?
Voici la définition trouvée sur Wikipedia:
« Un mélangeur statique est un dispositif de mélange en continu des fluides1. Ce dispositif permet de mélanger des liquides mais il peut aussi être utilisé avec des gaz ou pour mélanger un gaz et un liquide. Les dépenses énergétiques permettant de favoriser le mélange provoquent une perte de pression lors du passage du fluide à travers le mélangeur statique. »
En d’autres termes, il s’agit d’un tuyau dans lequel deux ou plusieurs fluides sont introduits et transportés à travers une série d’éléments « statiques » tels que des plaques ou des palettes pour homogénéiser les fluides à la sortie. Pourquoi est-ce une excellente application pour les additifs ? Parce que vous pouvez optimiser et personnaliser la conception pour toute application donnée. Pourquoi un mélangeur statique est-il une pièce difficile à produire de manière additive ? Parce que les éléments de mélange posent un problème lorsqu’ils sont imprimés selon les directives traditionnelles de l’AM. Les directives de conception standard pour l’AM signifient que ces éléments devraient être imprimés à des angles de 45 degrés. Cette limitation nécessiterait soit d’allonger la zone de mélange du mélangeur lui-même et/ou d’ajouter beaucoup plus d’éléments pour obtenir les performances souhaitées. Dans les deux cas, vous ne tirez plus parti des avantages de l’additif et il ne reste qu’une pièce inefficace et coûteuse.
Mélangeur statique avec : | Mélangeur statique AddUp | Standard AM Guidelines (45˙ fins) | Réduction |
---|---|---|---|
Hauteur totale | 305 mm | 654 mm | 53% |
Matériel nécessaire | 738.5 cc | 1583.82 cc | 53% |
Temps de construction | 88 heures, 32 minutes | 189 heures, 51 minutes | 53% |
Le mélangeur statique AddUp a augmenté la productivité de 53 % !
Et si vous n’aviez pas cette contrainte ?
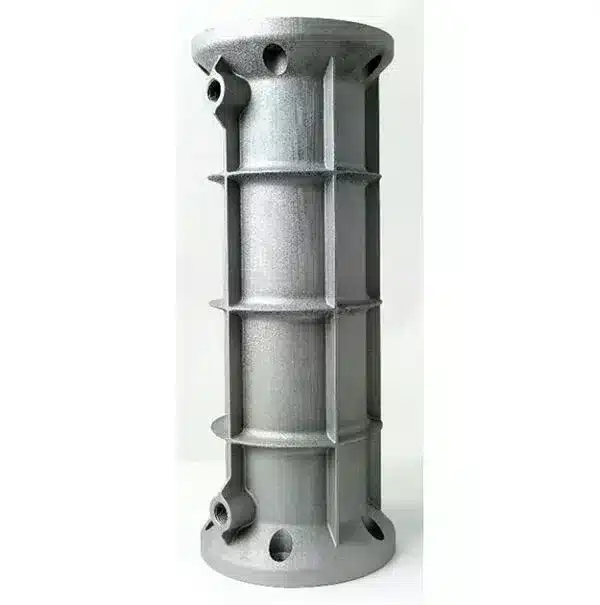
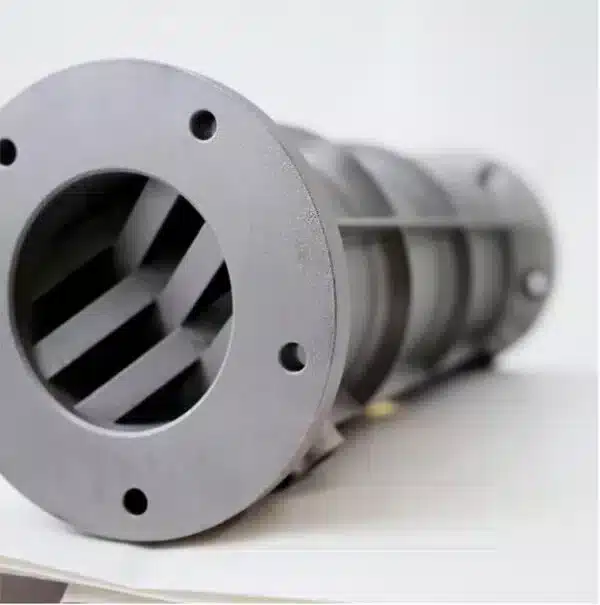
Le mélangeur statique présenté ici a été imprimé sans ces contraintes techniques. Nos ingénieurs ont conçu ce mélangeur avec des éléments aussi peu profonds que 25 degrés sans aucun support tout en obtenant un état de surface acceptable. De plus, ils l’ont conçu en moins de deux semaines et ont obtenu un rendement de premier ordre. Comment est-ce possible ? La configuration du rouleau et de la poudre fine d’AddUp, associée aux bons paramètres, offre de nouvelles libertés de design pour la technologie additive.
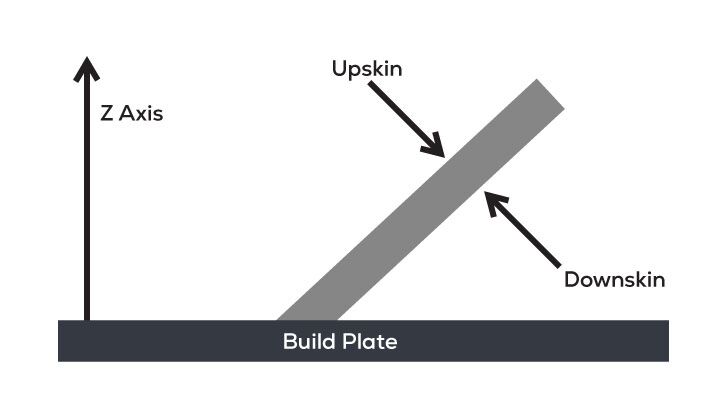
Comme le montrent les figures A et B, en utilisant un système de rouleaux avec une poudre plus fine, le système AddUp peut obtenir une réduction de la rugosité de surface d’environ 10 Ra μm pour tout angle upskin/downskin donné, par rapport aux à une poudre moyenne avec un système de mise en couche de type racleur. (Upskin : surface supérieure.. Downskin : surface inférieure).
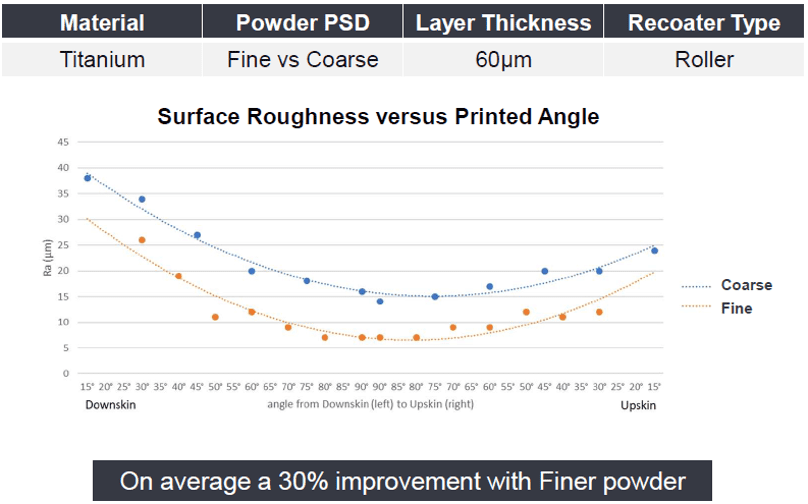
EXPOSITION A
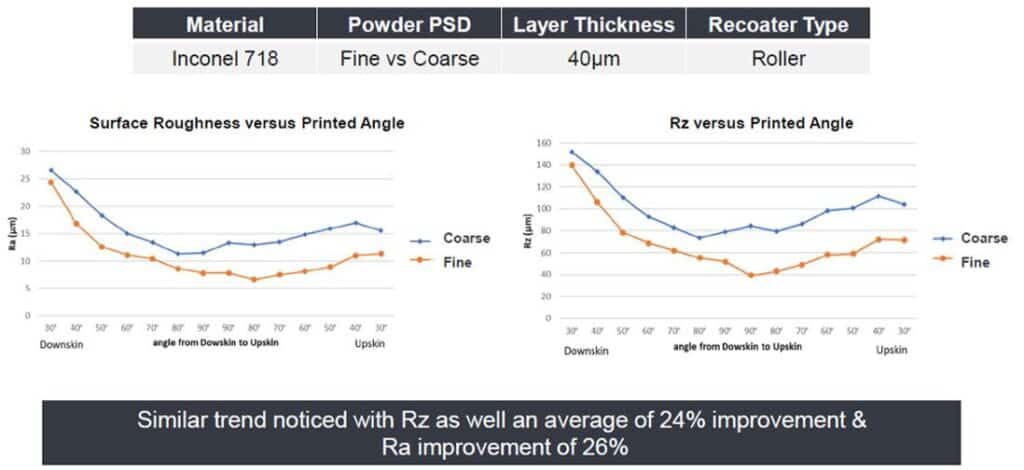
EXPOSITION B
N’oubliez pas que tout cela a été réalisé dès la sortie de la machine et sans aucun problème ! Il n’y a pas de paramètres spéciaux pour le downskin. Il n’est pas nécessaire de recourir à un développement avancé qui peut prendre des mois et d’innombrables heures d’ingénierie et de temps machine pour y parvenir. Ces résultats peuvent être obtenus à l’aide de nos paramètres standards. Chez d’autres fabricants de machines, les états de surface améliorés ou les inclinaisons extrêmes ont souvent pour conséquence de ralentir votre productivité. En effet, ils utilisent moins de puissance laser à une vitesse réduite pour obtenir de tels résultats, ce qui ralentit votre productivité. Cela introduit également des variables supplémentaires dans les propriétés mécaniques de votre pièce. Au lieu d’avoir un ensemble unique de paramètres, donnant un ensemble connu de propriétés mécaniques dans tout le volume de votre pièce, vous avez créé des zones qui peuvent potentiellement présenter des comportements différents. Le système AddUp obtient ces résultats grâce à une meilleure densité de remplissage de notre lit de poudre et à la configuration de notre rouleau à poudre fine.
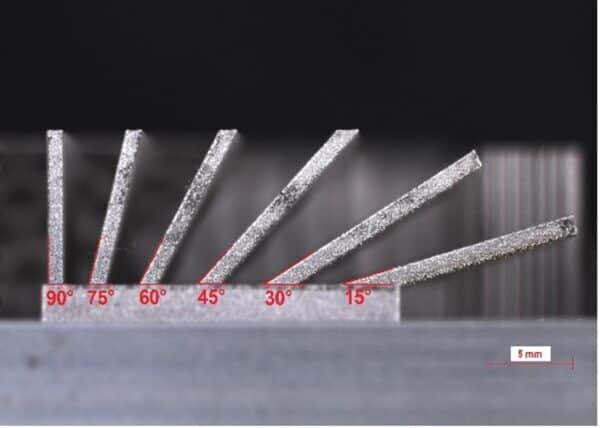
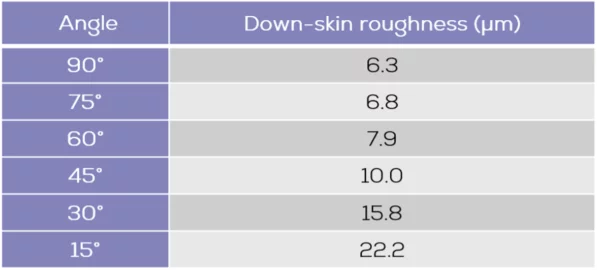
Vous pensez que c’est trop beau pour être vrai ? Venez faire un essai chez nous ! Nous venons d’achever la rénovation de nos installations de Cincinnati, qui servent non seulement de siège social aux États-Unis, mais aussi de centre de démonstration technique. De la poudre à la pièce, notre atelier dispose de toutes les capacités pour réaliser des prototypes fonctionnels et même imprimer en 3D des pièces en série. Notre équipe est prête à accompagner nos clients, qu’il s’agisse de se lancer dans l’AM ou de réaliser une application industrielle clé en main.
Utilisez le formulaire ci-dessous pour nous parler de votre projet et nous vous montrerons la différence AddUp ! Nous attendons avec impatience l’opportunité de travailler ensemble.