La fabrication additive métallique, en particulier la technologie de fusion laser sur lit de poudre (L-PBF), offre de nouvelles possibilités aux secteurs du moulage et de l’outillage. Elle permet de produire des moules à géométrie complexe, des pièces imbriquées et des canaux de refroidissement conformes, ce qui se traduit par une amélioration de la productivité, une réduction des temps de refroidissement et une amélioration de la qualité des pièces.
Les industriels des secteurs du moulage et de l’outillage font aujourd’hui un usage intensif de la fabrication additive. Ils utilisent l’impression 3D plastique pour la réalisation de moules prototypes ou de moules à cire perdue, l’impression 3D de sable pour la fabrication d’inserts, ou encore la stratification de couches pour réaliser des moules à étages. La fabrication additive métallique, quant à elle, connaît un développement moins rapide. Pourtant, la technologie de fusion laser sur lit de poudre (L-PBF) présente plusieurs atouts intéressants pour ces secteurs.
De nouvelles applications dans le domaine de l’injection
La technologie L-PBF propose plusieurs voies d’amélioration des procédés d’injection. On parle ici de moules métalliques utilisés pour produire des pièces en plastique. D’abord, la capacité du procédé L-PBF à produire des pièces aux géométries complexes permet d’envisager de nouvelles formes. Pour les parois moulantes, c’est-à-dire les parties du moule qui sont en contact avec la pièce plastique, les possibilités de gains en complexité sont limitées, pour deux raisons : la nécessité d’accéder aux surfaces avec des outils d’usinage et de polissage pour réduire leur rugosité, et le respect des angles de dépouille, car les formes du moule doivent permettre le démoulage de la pièce.
Néanmoins, des pistes restent à explorer. Comme la technologie L-PBF permet de fabriquer des pièces imbriquées les unes dans les autres, les concepteurs de moules peuvent imaginer de nouveaux types de mouvements à l’intérieur de leurs moules, en plaçant des « tiroirs » (éléments mobiles) dans des zones jusqu’ici impossibles à atteindre avec les techniques conventionnelles. En matière de fiabilité, également, des gains sont possibles. Les éléments assemblés par soudage ou vissage sont en général les points faibles des moules utilisés en grande série, et l’impression 3D métallique offre la perspective de les réaliser en une seule opération, et donc d’améliorer leur durée de vie.
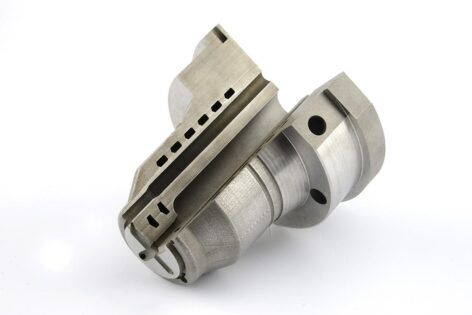
Les industriels qui envisagent d’utiliser la fabrication additive métallique pour réaliser des moules d’injection doivent garder à l’esprit que la technologie L-PBF est peu adaptée à la réalisation de pièces massives, pour des raisons de coûts mais aussi d’accumulation de contraintes thermiques. Il faudra donc éviter de l’employer pour produire des moules complets, et limiter son utilisation aux zones pour lesquelles elle présente un intérêt.
Cette contrainte, qui pourrait sembler un frein au déploiement de cette technologie dans les moules, offre au contraire des perspectives intéressantes. En effet, concevoir des moules dont la partie massive est standard et la partie proche de la paroi moulante est imprimée présente des avantages. D’abord, c’est la possibilité d’effectuer des changements de séries plus rapides, car les délais d’obtention des moules sont en général de plusieurs mois. Ensuite, c’est l’opportunité de réduire les immobilisations, car le stockage des parties imprimées représente moins de volume que le stockage des moules complets. Enfin, c’est la perspective d’envisager des fabrications en petites séries qui n’auraient pas été rentables au vu de l’investissement dans un moule complet. Voire, à terme, de tendre vers la fabrication de produits personnalisés, un univers aujourd’hui difficilement accessible pour les pièces en injection plastique.
Des gains de productivité et de qualité
Avant de penser à utiliser l’impression 3D métallique pour développer de nouveaux produits et services, il peut être utile de l’employer pour améliorer l’existant. En effet, l’une des applications phare de la technologie L-PBF dans le monde du moule d’injection est une technique appelée « conformal cooling ». Elle consiste à optimiser les temps de refroidissement des pièces plastiques dans les moules d’injection, par la création de canaux épousant la forme de la pièce à refroidir. Ces canaux placés au plus près de la paroi moulante permettent de réduire les temps de refroidissement, et donc d’augmenter les cadences de production. En effet, dans un cycle d’injection, l’étape de refroidissement de la matière est en général l’étape qui dure le plus longtemps. C’est donc en réduisant ce temps que l’on peut obtenir les gains de productivité les plus importants. Des gains sont aussi possibles sur l’aspect des pièces injectées, car placer des canaux dans les zones d’ordinaire difficiles à refroidir permet d’éviter les phénomènes de retassures ou les lignes de soudure, qui sont des problèmes dus à un refroidissement non optimal.
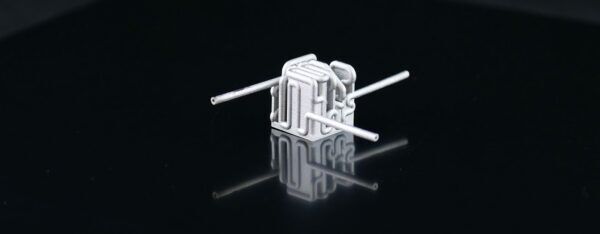
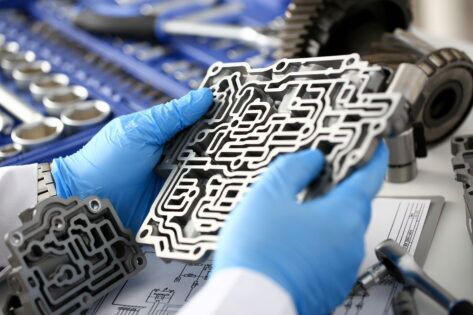
Si les ingénieurs qui conçoivent les moules d’injection peuvent depuis toujours imaginer des circuits de régulation aux formes complexes, ils étaient jusqu’ici limités par les techniques de fabrication des moules. Pendant longtemps, les seules techniques disponibles pour créer des canalisations dans un bloc de métal ont été la technique du perçage, de l’usinage, et la technique de stratification de couches (on conçoit le moule par couches distinctes, chacune des couches est fraisée et percée afin que l’assemblage des couches donne naissance à des canalisations en trois dimensions).
Aujourd’hui, avec les techniques de fabrication additive par fusion laser sur lit de poudre, les fabricants de moules accèdent à une totale liberté de conception pour leurs canaux de régulation. A ce propos, on notera que les états de surface des pièces produites par fusion laser sur lit de poudre sont particulièrement adaptés à la création de canaux de refroidissement : suffisamment lisses pour ne pas générer de turbulences dans les canaux, mais suffisamment rugueux pour augmenter la surface d’échange par rapport à des canaux réalisés par perçage.
Autre avantage de conformal cooling : en plaçant des canaux de régulation au plus près de l’empreinte du moule, on réduit le volume total de métal à refroidir. Cela permet au moule d’atteindre plus rapidement sa température de fonctionnement. Ainsi, le temps entre la mise sous tension de la machine et la sortie de la première pièce bonne se trouve réduit, ce qui entraîne des gains de productivité et une réduction du nombre de pièces défectueuses.
Des outils d’aide à la production
Quelles que soient les raisons qui poussent un industriel à s’intéresser à l’impression 3D, on constate toujours que l’expérience acquise dans le cadre d’un projet fait naître d’autres idées, parfois dans d’autres services de l’entreprise. Des gains importants peuvent être générés si l’on voit au-delà des produits vendus aux clients et des moules nécessaires pour les fabriquer, en considérant l’outil de production dans sa globalité. En effet, dans tout atelier de production, il existe une multitude de tâches qui peuvent être simplifiées, améliorées ou sécurisées grâce à des outils réalisés sur mesures. Depuis les gabarits qui facilitent les opérations d’assemblage, jusqu’aux détrompeurs qui évitent les erreurs lors du montage, en passant par des outils à main allégés dont les poignées sont adaptées à la main de chaque opérateur… La fabrication additive offre de nombreux moyens pour réduire les temps de production, améliorer la qualité des produits, ou diminuer le risque de TMS (troubles musculosquelettiques).
Il en va de même pour les industriels qui utilisent des robots, ou exploitent des lignes d’assemblage automatisées : chaque fois qu’une pièce en mouvement peut être allégée, cela entraîne moins de vibrations, moins d’usure, une consommation énergétique diminuée, et des temps de production réduits. La fabrication additive fournit des réponses à ces applications d’allègement, par la création d’évidements à l’intérieur des volumes, par la création de structures légères (structures lattices) ou par la méthode de l’optimisation topologique.
Pour développer toutes ces applications « indirectes » de la fabrication additive, et l’utiliser pour fabriquer des « outils » au sens large du terme, une bonne pratique consiste à encourager tous les opérateurs et les techniciens à partager la culture de la fabrication additive dans l’entreprise, pas seulement dans les bureaux d’études, ceci afin que tous les collaborateurs soient capables de proposer des idées d’amélioration de l’outil de production.
Conclusion
Les applications de la fabrication additive métallique dans le domaine de l’outillage devraient continuer de se développer dans les années à venir, d’autant que des progrès sont faits tous les jours sur la productivité, la maîtrise du procédé et le développement de recettes pour les métaux utilisés traditionnellement par les industriels du secteur. Ces applications seront très variées, car elles pourront porter tant sur les temps d’industrialisation, sur la qualité des pièces, sur les cadences de production, sur les immobilisations que sur les services délivrés aux clients.