Der 3D-Druck von Metall unter industriellen Produktionsbedingungen ist die Lösung für die Herausforderungen der Luftfahrt, um ihre Wettbewerbsfähigkeit zu erhalten und zu steigern.
AddUp und Dassault Aviation arbeiten zusammen, um die additive Fertigung von Metallen in der Luftfahrt vom „Prototyping“ zur „Massenproduktion“ zu bringen. Um dies zu erreichen, muss die additive Technologie optimiert werden, um ihre Fähigkeiten in Bezug auf Qualität, Reproduzierbarkeit und Produktivität zu demonstrieren, um die Massenproduktion von Metallteilen zu ermöglichen, die dann in Flugzeuge integriert werden.
Die Luftfahrtindustrie steht vor vielen Herausforderungen, um ihre Wettbewerbsfähigkeit zu erhalten und zu steigern: der wachsende weltweite Luftverkehr, die zunehmende Materialknappheit, die Verschlankung und Optimierung von Teilen, die Suche nach Zuverlässigkeit für bessere Qualität und die Einhaltung immer anspruchsvollerer Vorschriften sind alles Fragen, die heute gelöst werden müssen. Eine der Antworten auf diese Herausforderungen ist der Einsatz des 3D-Drucks von Metall unter industriellen Produktionsbedingungen.
In diesem Zusammenhang wurde das kollaborative F&E-Projekt „AEROPRINT“, das von Dassault Aviation koordiniert wird, mit Hilfe zahlreicher Partner, Forschungszentren, Universitäten und Industrien, zu denen auch AddUp gehört, ins Leben gerufen. Dieses auf 5 Jahre angelegte Projekt zielt darauf ab, einen wettbewerbsfähigen vorindustriellen Demonstrator für die additive Fertigung von Multimaterialien (Titan und Aluminium) zu entwickeln, zu qualifizieren und zu implementieren, um komplexe Flugzeugteile der Klassen 2 und 3 zu fertigen. Der Standort von Dassault Aviation in Argonay in der Region Auvergne-Rhône-Alpes (Frankreich) wurde als Pilotprojekt für die Umsetzung dieses Prozesses ausgewählt.
AddUp, ein Hersteller von Maschinen und additiven Teilen, ist mit der Entwicklung eines neuen Produktionssystems beauftragt, das auf Interoperabilität und Robotisierung von Prozessen basiert. Eine echte automatisierte Werkstatt, die es dank der additiven Technologie ermöglicht, Teile für die Luftfahrt in Serie und aus zwei verschiedenen Materialien herzustellen. Ziel ist es, die Geräte zu bündeln und gleichzeitig die Trennung und den richtigen Umlauf der beiden gewählten Materialien zu gewährleisten. Die Experten von AddUp arbeiten an einer neuen Art von geschlossenem Gehäuse, bei dem das Pulver auf der einen Seite hineingelangt und ein Tablett mit Metallteilen auf der anderen Seite herauskommt. Diese künftige Werkstatt wird aus zwei Produktionseinheiten mit vier FormUp® 350-Maschinen bestehen, die auf der Pulverbettschmelztechnologie (L-PBF: Laser Powder Bed Fusion) basieren, sowie aus den erforderlichen Nachbearbeitungsmitteln. Wir haben uns für zwei PBF-Maschinen von AddUp entschieden.
Nach einer Phase der gemeinsamen Forschung und Entwicklung, um alle Anforderungen dieses Projekts zu erforschen, arbeitet AddUp nun an dem Modell in Originalgröße, um die beibehaltenen Prinzipien zu verifizieren und zu validieren, von der mechanischen Konstruktion bis zur Autonomie, ohne dabei den Computer zu vergessen, denn alles wird vom Computer gesteuert. Der AddUp Manager mit seiner ergonomischen und intuitiven Benutzeroberfläche, die mit einer ultraschnellen Engine zur Generierung von Trajektorien ausgestattet ist, ermöglicht die Vorbereitung von Produktionsdateien durch den Zugriff auf mehr als 250 modifizierbare Variablen und anpassbare Fusionsstrategien. Das Monitoring, das für ein solches Projekt von zentraler Bedeutung ist, wird mit der bereits verfügbaren Software AddUp Dashboards durchgeführt und durch speziell für diesen Zweck entwickelte Bausteine erweitert.
Mit AddUp Dashboards können Sie alle Produktionsdaten in Echtzeit einsehen, die Werkstatt überwachen und jedes Maschinenereignis schnell analysieren. Zu den vielen vorkonfigurierten Ansichten, die die Software bietet, gehört eine anpassbare Karte, die den Fortschritt in Echtzeit, die verbleibende Produktionszeit und den aktuellen Status anzeigt. Die Benutzer können so auf die Daten eines Produktionslaufs zugreifen, der einige Monate zurückliegt, und die laufende Produktion über dasselbe Tool verfolgen.
Wie funktioniert dieser automatische Workshop?
Die beiden Metallpulver, die in industriellen Behältern verpackt sind, werden von einem Mitarbeiter an einer Lieferstation außerhalb der Werkstatt geladen. Im Inneren wird das Produktionstablett von einer automatischen Konditionierungsstation übernommen, die es in eine mobile Kammer, den sogenannten „Mantel“, einführt. Es wird in einem inerten Shuttle von einem Automated Guided Vehicle (AGV) transportiert und dann je nach gewünschtem Material in jede PBF-Maschine gelegt. Wenn der Druckvorgang abgeschlossen ist, holt das Shuttle die mobile Kammer zurück und bringt sie zu einer Entladestation.
Dieselbe Station ermöglicht es, den Großteil des während des Drucks nicht geschmolzenen Pulvers zu entfernen und es nach einer Recycling-Phase für den nächsten Druck zurückzuschicken. Sobald das Pulver vollständig entfernt ist, fährt das Shuttle zur Konditionierungsstation, wo das Tablett mit den Teilen aus der Kammer herausgezogen wird, um zur Wasch- und Trocknungsstation für die Teile zu gelangen. Letztere erhält ein neues Fach und beginnt erneut zu drucken. Das Tablett mit den Teilen wird feiner gereinigt, bevor es die Werkstatt verlässt und vom Bediener in Empfang genommen wird.
Es gibt viele Vorteile einer automatisierten Werkstatt. Aus HSE-Sicht (Gesundheit, Sicherheit und Umwelt) kommen die Bediener überhaupt nicht mit dem Pulver in Berührung. Sie betreten das robotergestützte Gehäuse nur für Wartungsarbeiten und erledigen ihre Aufgaben außerhalb des Gehäuses. Aus industrieller Sicht ist die Wiederholbarkeit der Produktion gewährleistet, sobald der Prozess validiert und qualifiziert wurde.
Diese automatisierte Vorläuferwerkstatt wird die Grundlage für eine sofort einsatzbereite Industrielösung für den Einsatz von Maschinen zur additiven Fertigung in bestehenden Werkstätten bilden, die ein Höchstmaß an Produktivität und Sicherheit gewährleistet.
Über Dassault Aviation
Der Werkzeugbau ist unsere Leidenschaft. Mit mehr als 10.000 militärischen und zivilen Flugzeugen, die im vergangenen Jahrhundert in mehr als 90 Länder geliefert wurden, verfügt Dassault Aviation über anerkannte Expertise und Erfahrung in Design, Entwicklung, Verkauf und Support aller Arten von Flugzeugen, vom Rafale-Kampfflugzeug bis hin zur Falcon-Familie von High-End-Geschäftsjets und militärischen Drohnen. Im Jahr 2017 belief sich der Umsatz von Dassault Aviation auf 4,8 Milliarden Euro. Die Gruppe hat 11.400 Mitarbeiter.
Mitglieder des Aeroprint-Konsortiums:
- Industrielle Partner: Dassault Aviation, Constellium, AddUp, Alprobotic, Tekna und Comefor von der WeAre Aerospace Gruppe
- Technologie-Ressourcenzentren: CEA Tech, Manutech
- Akademische Partner: INP Grenoble, Ecole des Mines de Saint-Etienne, SIGMA Clermont und INSA Lyon
- Cluster für die Wettbewerbsfähigkeit: CIMES
Die 4 wichtigsten Meilensteine des AEROPRINT:
2021: Start der Demonstrationswerkstatt am Standort Argonay
2022: erste industriell gefertigte Teile durch additive Fertigung
2024: Teile, die mit optimierter additiver Fertigung und robotergestützter Nachbearbeitung hergestellt werden
2025: Roboterisierte Werkstatt und Herstellung von für die Luftfahrt zertifizierten Demonstratorteilen
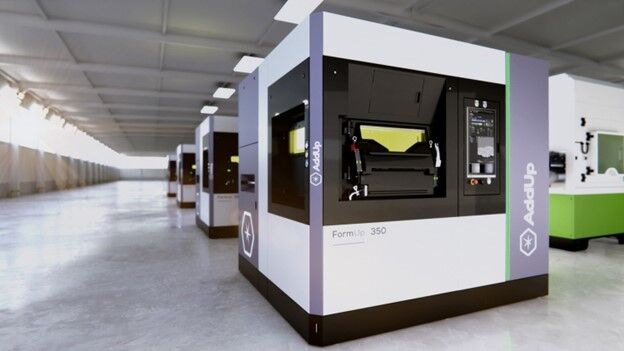